Helm Wind
Led by E.ON, the consortium also included BP, Rolls-Royce and the University of Strathclyde
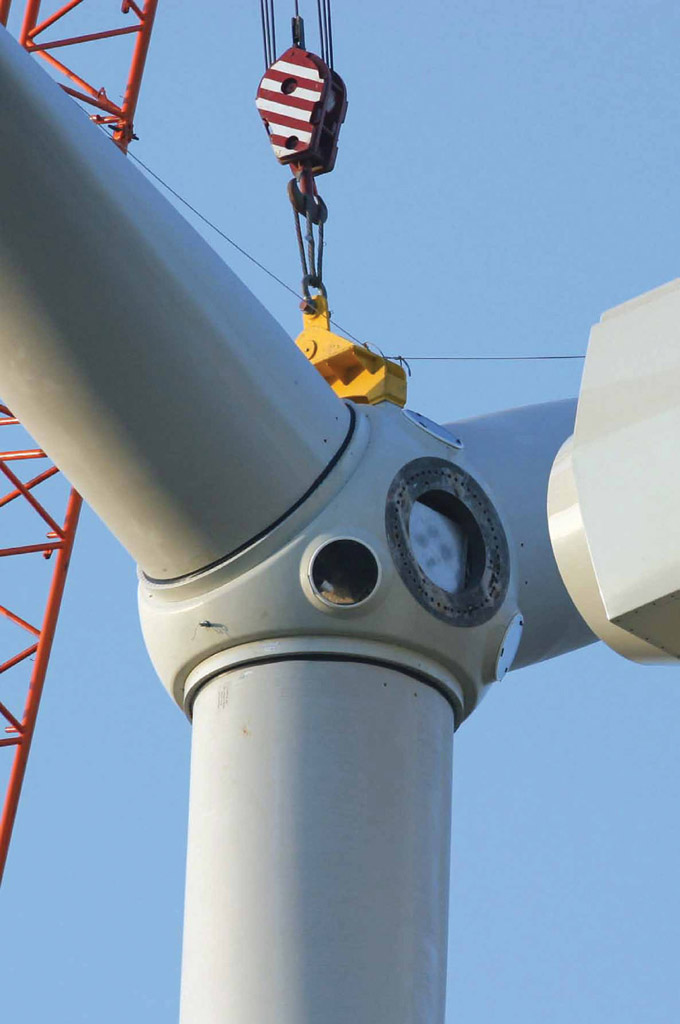
About the project
- Investigation into concepts and technologies required to deliver significant cost reductions
- Swept areas (blade size) needed to be larger than was usual at the time of the project
- The optimum size of turbine identified was larger than the historical state of the art design
The Helm Wind project carried out an unconstrained investigation into the concepts and technologies required to deliver significant cost of energy reductions for offshore wind. This included rotor diameter, geometry and speed, number of blades, upwind and downwind orientations, drivetrain options and support structures. Led by E.ON, the consortium also included BP, Rolls-Royce and the University of Strathclyde.
The project started in January 2009 with an ETI investment of £2.5m. The project finished in the autumn of 2010. It identified that sufficient improvements could be made through technology innovation to deliver energy costs that were comparable with 2010 onshore wind costs one of ETI objectives for the offshore wind programme.
This required innovation in rotor aerodynamics and diameter, drivetrain technologies and electrical systems. The consortium also identified that the optimum turbine size for offshore wind; was significantly larger than the historical state of the art design.